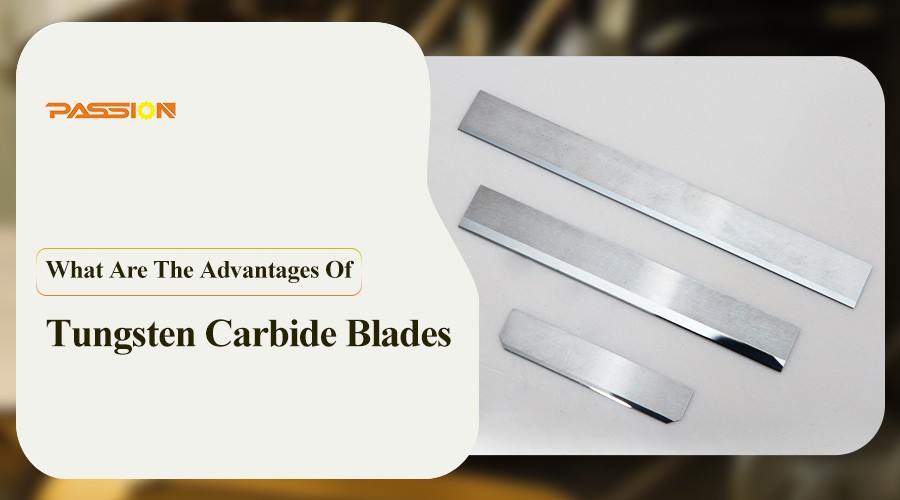
In many fields such as metal processing, wood cutting, stone quarrying, etc., the choice of cutting tools is directly related to production efficiency and product quality. Tungsten Carbide Blades, as a high-performance cutting tool, are gradually becoming the first choice of many industries due to their unique advantages. In this article, we'll take an in-depth look at some of the key benefits of Tungsten Carbide Blades, and reveal why they've gained a significant foothold in the marketplace.
The biggest advantage of Tungsten Carbide Blades is their extremely high hardness and wear resistance. Tungsten carbide, a hard alloy consisting of tungsten carbide particles with a metallic cobalt or other metal binder, is second only to diamond in hardness, and much harder than conventional high-speed steel and stainless steel. This enables tungsten carbide inserts to maintain their sharpness for a longer period of time during the cutting process, effectively reducing cutting resistance and cutting time, and significantly improving machining efficiency. At the same time, the high wear resistance of tungsten carbide also ensures that the inserts are less prone to wear over a long period of time, prolonging their service life and reducing the frequency of replacement, thus reducing production costs.
In addition to hardness and wear resistance, Tungsten Carbide Blades have excellent heat and corrosion resistance. In high-speed cutting and high-temperature environments, Tungsten Carbide Blades are able to maintain stable mechanical properties and are not easily softened or deformed by high temperatures, which ensures the precision and stability of cutting. In addition, tungsten carbide inserts also have excellent corrosion resistance, able to resist the erosion of a variety of chemical substances, suitable for a wider range of cutting materials.
Another significant advantage of Tungsten Carbide Blades is their good toughness and impact resistance. While maintaining high hardness, tungsten carbide inserts also have a certain degree of toughness, able to withstand large cutting forces and impacts, and not easy to chip or break. This makes tungsten carbide inserts perform better when cutting hard materials or roughing.
In addition, Tungsten Carbide Blades have good machinability and customizability. Tungsten carbide inserts can be customized in precise size and shape to meet specific cutting requirements for a variety of complex cutting tasks. Tungsten carbide inserts are also easy to sharpen and repair, which extends their service life and improves their cost-effectiveness.
Tungsten Carbide Blades also excel when it comes to environmental friendliness and sustainability. The long life of tungsten carbide inserts reduces the frequency of cutting tool replacement, which in turn reduces waste generation. In addition, Tungsten Carbide is a recyclable material that can be recycled to reduce resource waste and environmental pollution.
In summary, Tungsten Carbide Blades have become the preferred cutting tools in many industries due to their high hardness, wear resistance, heat resistance, corrosion resistance, toughness, machinability and environmental friendliness. With the continuous progress of technology and the sustained development of manufacturing industry, Tungsten Carbide Blades will play an important role in more fields and promote industrial manufacturing to a more efficient and environmentally friendly direction.
Later, We will continue to update information, and you can find more information on our website (passiontool.com) blog.
Of course, you can also pay attention to our Official social media:
Post time: Feb-10-2025